Introduction
Diesel generators play a crucial role in providing backup power in a wide range of applications, from industrial facilities to residential homes. The performance of a diesel generator is essential to ensure reliable and efficient operation during power outages. Performance analysis of diesel generators involves evaluating various parameters and factors that impact their efficiency, reliability, and overall performance.
This article provides a comprehensive guide to diesel generator performance analysis, covering key aspects such as fuel consumption, load capacity, efficiency, maintenance, and monitoring. By understanding these factors and how they influence the performance of diesel generators, operators and maintenance personnel can optimize their operation and ensure reliable power supply when needed.
1. Fuel Consumption Analysis
Fuel consumption is a critical factor in the performance of diesel generators, as it directly impacts operating costs and efficiency. The fuel consumption of a diesel generator is influenced by various factors, including generator size, load demand, engine efficiency, and operating conditions. Analyzing fuel consumption data can help operators optimize generator usage and identify opportunities for fuel savings.
One key metric used to analyze fuel consumption is the specific fuel consumption (SFC), which is the amount of fuel consumed per unit of power output. Lower SFC values indicate greater fuel efficiency, while higher values suggest inefficiencies in the generator's operation. Monitoring SFC over time can help identify trends and potential issues that may be affecting fuel consumption.
In addition to SFC, operators should also consider factors such as fuel quality, engine maintenance, and operating conditions when analyzing fuel consumption. Regular fuel quality testing and engine tune-ups can help ensure optimal performance and efficiency, while monitoring load demand and operating hours can help identify opportunities for fuel savings.
2. Load Capacity Analysis
The load capacity of a diesel generator refers to its ability to handle varying levels of electrical load while maintaining stable operation. Understanding the load capacity of a generator is essential to avoid overloading or underloading, which can lead to decreased efficiency, increased wear and tear, and potential damage to the generator.
Load capacity analysis involves determining the maximum load that a generator can handle under different operating conditions. This includes analyzing the generator's rated capacity, standby capacity, and overload capacity to ensure that it can meet the power demands of the connected load without exceeding its limits.
Operators can use load profiling and load testing to evaluate the load capacity of a diesel generator in real-world conditions. Load profiling involves monitoring and recording the electrical load demand over time to identify peak load periods and load fluctuations. Load testing involves simulating different load scenarios to determine how the generator responds to varying levels of demand.
By conducting 150kw diesel generator for events , operators can ensure that the generator is properly sized for the intended application, identify potential load-related issues, and optimize the generator's performance under different operating conditions.
3. Efficiency Analysis
Efficiency is a key performance metric for diesel generators, as it directly impacts operating costs, fuel consumption, and environmental impact. Diesel generator efficiency is influenced by factors such as engine design, fuel quality, maintenance practices, and operating conditions. Analyzing the efficiency of a generator can help identify opportunities for improvement and cost savings.
One common measure of efficiency for diesel generators is the fuel efficiency ratio (FER), which is the ratio of electrical power output to fuel input. Higher FER values indicate greater efficiency, while lower values suggest inefficiencies in the generator's operation. Monitoring FER over time can help operators identify trends and make adjustments to improve efficiency.
In addition to FER, operators should also consider factors such as heat rate, thermal efficiency, and overall system efficiency when analyzing the performance of a diesel generator. Regular maintenance, tuning, and monitoring of key performance indicators can help optimize efficiency and reduce operating costs over the life of the generator.
4. Maintenance Analysis
Proper maintenance is essential to ensure the reliable and efficient operation of diesel generators. Maintenance analysis involves evaluating the condition of key components, identifying potential issues, and implementing preventive maintenance strategies to avoid downtime and costly repairs.
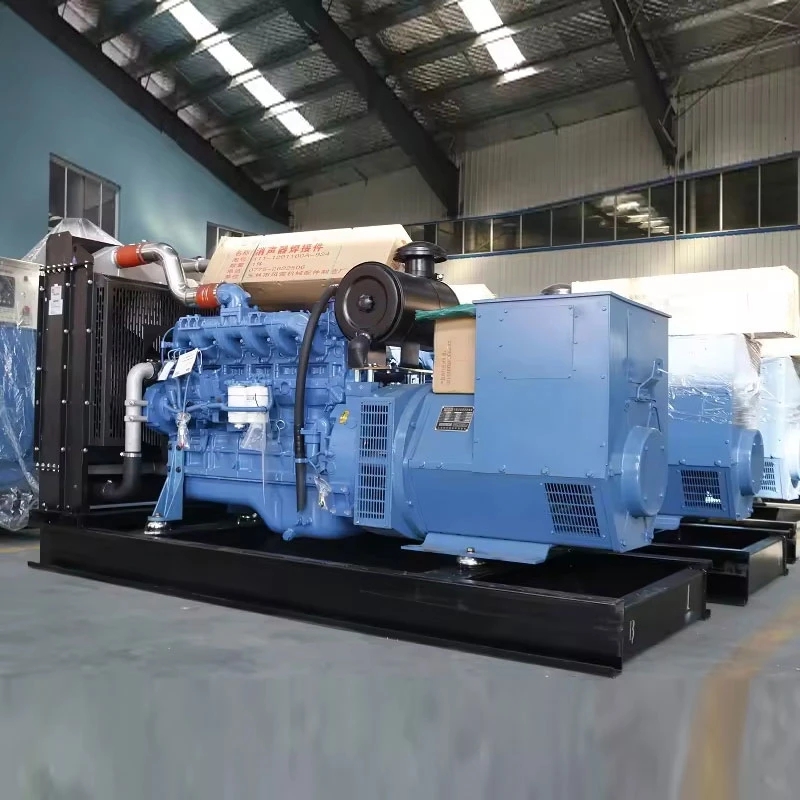
Key maintenance tasks for diesel generators include regular oil and filter changes, coolant system maintenance, fuel system cleaning, and inspection of critical components such as belts, hoses, and electrical connections. By conducting routine maintenance and inspections, operators can identify and address issues before they escalate into major problems.
Monitoring key performance indicators such as oil pressure, coolant temperature, and exhaust emissions can help operators identify potential maintenance issues and take corrective action. Implementing a comprehensive maintenance schedule that includes regular inspections, testing, and component replacements can help ensure the long-term performance and reliability of a diesel generator.
5. Monitoring and Control Analysis
Monitoring and control systems play a crucial role in the performance analysis of diesel generators, as they provide real-time data on key operating parameters and allow operators to make informed decisions to optimize performance. Monitoring systems can track parameters such as fuel consumption, load demand, engine temperature, and system efficiency to help operators identify issues and trends.
Control systems allow operators to adjust settings, switch between power sources, and implement load shedding strategies to optimize the operation of the generator. By using advanced monitoring and control systems, operators can improve efficiency, reduce downtime, and ensure reliable power supply during emergencies.
Remote monitoring and control systems enable operators to monitor and control diesel generators from a central location, allowing for proactive maintenance, troubleshooting, and performance optimization. By leveraging the latest technologies in monitoring and control, operators can maximize the performance and reliability of their diesel generators.
Conclusion
Diesel generator performance analysis is essential to ensure reliable and efficient operation in a wide range of applications. By evaluating key factors such as fuel consumption, load capacity, efficiency, maintenance, and monitoring, operators can optimize the performance of their generators and ensure reliable power supply when needed. Implementing a comprehensive performance analysis strategy that includes regular monitoring, maintenance, and control can help maximize the lifespan and efficiency of diesel generators, ultimately saving costs and improving overall reliability.